Why Is Oil Cleanliness Important?
Maintaining oil cleanliness is critical to the success of industrial operations. Oil contamination from particulate matter accelerates the rate of component wear and can lead to premature component failure. But why is cleanliness so important? In a globally competitive market, it is imperative that companies can maintain a precise level of machine reliability and uptime to keep costs at a competitive level. Clean, contaminant-free oil will extend the lifetime and the overall reliability of the equipment.
The reporting standard for fluid cleanliness is ISO4406:99. A code number is assigned to particle count values at three different micron levels per 1 ml of fluid:
- Greater than 4 microns
- Greater than 6 microns
- Greater than 14 microns
The code is assigned based on the table below:
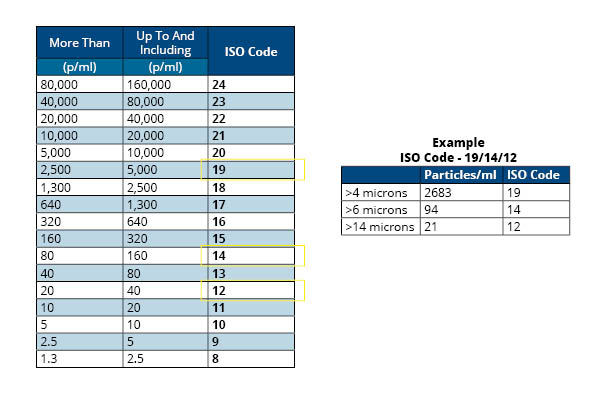
Generally, when you increase in the code, the number of particles has doubled.
Remember, the ISO code is the tool to use for setting targets, alarms, and cleanliness goals. It is also great to use as a key performance indicator [KPI]. But it should not be the only thing used when it comes to evaluating your oil analysis data. For instance if you have a target cleanliness level of 19/17/14, your previous sample was 18/16/13 yet your most current sample is 19/17/14. You've achieved your cleanliness target, and suggests that your component is in normal status, but, there has been an increase in particles into your equipment.
Where Can Contamination Enter The System
Contamination can enter your system in different ways such as:
- Built-in contamination - this is contamination that occurs during the construction of the machine or piece of equipment.
- Generated contamination - occurs from the wearing of components; these contaminants are typically removed through proper filtration
- Ingress contamination - this is contamination that enters your system from the outside. This could be from adding new unfiltered oil or particles entering from the system being opened
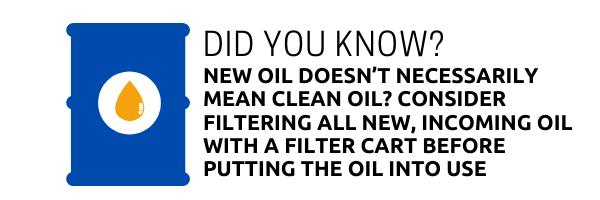
Contamination particles need to be removed from your system with an effective filtration system.
How Checkfluid Can Protect Your Equipment At Every Stage
Checkfluid products can help you keep contamination out of the system and can help you effectively control contamination.
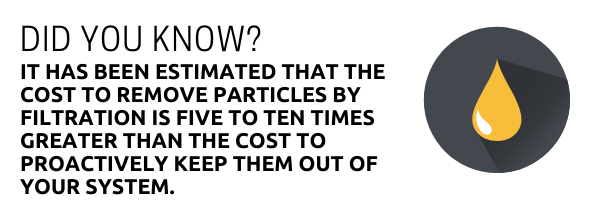
Let's start with the incoming oil. Checkfluid's Drum/Tote Adapter will let you clean, monitor and transfer your new oil. The Drum/Tote adapter is installed into your drum or oil tote. The two quick connects allows the user to hook up to a portable filter cart or filtration system, to clean the new oil. These quick connects also allow you to cleanly connect to transfer containers. This closed transfer system reduces the risk of contaminants getting into the oil or machine. The high flow sampling valve allows you to continually check on your oil without opening the drum up to external contamination. While the optional desiccant breather provides additional protection from moisture and particulate contamination.
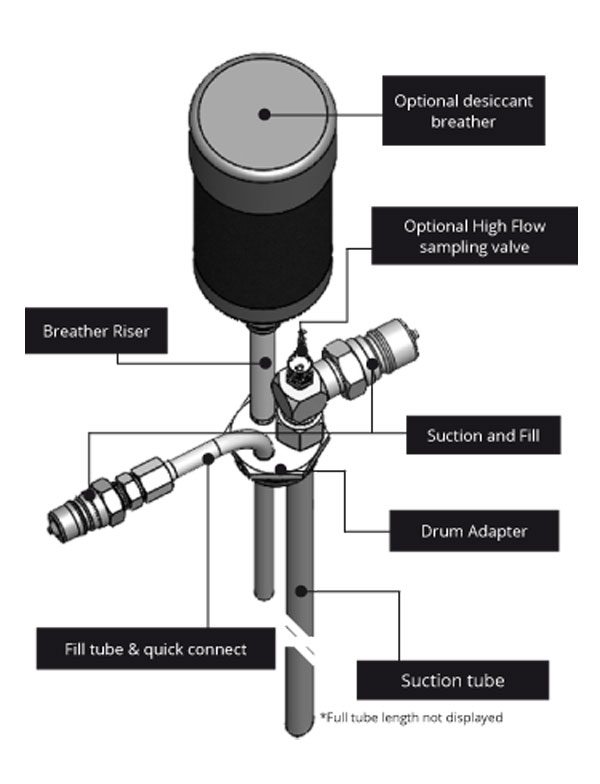
Drum/Tote Adapter - Full tube length not displayed
For your equipment consider the CORE Solution.
Checkfluid’s CORE Solution combines Checkfluid’s AB Breather Mount with the AD Drain Mount for a closed monitoring system. The AB Breather Mount allows the user to mount a desiccant breather, while maintaining fill and filtering capabilities. The quick coupling can be used for both topping up the system and connecting to a filter cart. The AD Drain Mount is installed into the drain port. It allows the user to add visual inspection tools alongside a permanent sampling tube ensures that the oil samples taken are representative, away from bottom and side sediment, as close to the active zone as possible. The quick coupling can be used for both draining and connecting to a filter cart. A kidney loop can be set up, connecting the AD and the AB together through the vent kit of the level gauge.
Preventative production-friendly Installs and most any gearbox or reservoir. To get started contact Checkfluid.