Final Drive Sampling
Contamination dirt and water, overheating caused by leaks, underfilling, or overfilling are leading causes of premature seal, bearing, and gear wear. This results in lost production and expense in construction and mining sites around the world. Each factor combines with the others to cause an incipient spiral into early failure mode. Many people are unaware that removing the plug adds a significant level of contamination into the system. Larger windblown sand or dirt particles become ground down to smaller particles which can now enter the contact points of bearings and gear sets
How To Sample Final Drives
The LE is essentially a drain plug with an embedded and compact flush face, high flow valve, equipped with a protective cap that can draw oil without opening up the system to dirt and dust. The LEM version includes a short sampling tube and magnet.
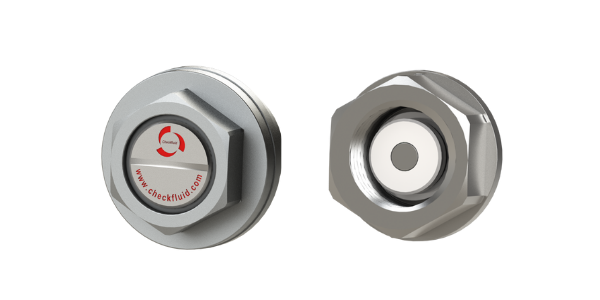
Installing an LE Series valve provides a great opportunity for regular clean sampling of gear oil. Gear oil should generally be checked every 100 hours or approximately once a month. Simply replace the drain plug with an LE Series valve plug to take advantage of a variety of method improvements. Vacuum sampling through an LE valve avoids opening up the drive through a vent port or plug to atmospheric contamination. It avoids the difficulty of dropping curled tubing to a midpoint location without scraping the sides and introducing contamination into the sample.
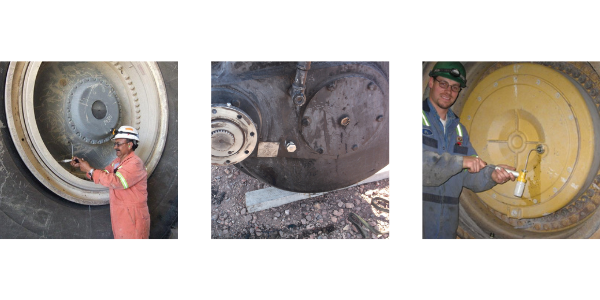
As an extra step forward, Checkfluid is now introducing a new LV vacuum charged bottle to take a sample from the LE plug without needing a vacuum pump. Vacuum pumps can be a source of contamination or cross-contamination in the field. Care must be taken to keep the valves, bottles and tubing clean during the process. The LV bottle is much faster and convenient and helps avoid this contamination especially when opening and closing the bottle.
Even before unthreading the valve cap, consider using a lint-free cloth to clean around the area minimizing the chance of particulate entering the drive or the sample.
Draining
To drain, simply remove the entire valve plug. Using the LEM version with the high-strength magnet provides another visual to indicate ferrous debris associated with premature wear at the time of draining.
Oil Level Checking
If there is also a level plug, the LE/LEM on the wheel can be rotated using the Drive Position Indicator (DPI) to a more precise position to check for the correct oil level even when the equipment is sloped up or down. Even a small drop in oil level would indicate a possible leak source that should be investigated for seal damage and as an ingress point for contamination.
For small top-ups, using the Checkfluid's Top Up Pump, several ounces can be added cleanly to the system through the LE valve and measured.
Safety
When opening up a working system for servicing, heat can build up in the airspace of the drive. An overheated headspace can cause a plug to launch creating a personal danger to the technician. The LE/LEM valve plug and probe can be used to relieve the pressure safely.
We are also actively working on a final drive filtration solution.
What is the Drive Position Indicator (DPI)?
The DPI is the first system developed with the sole purpose of orienting the drive axles for service. Precisely position the drive to fill, drain, level check, or sample in seconds - saving 5-10 minutes of time on each wheel by avoiding multiple forward/backward adjustments.
The DPI becomes invaluable when it becomes time to drain the oil as it can line up the valve plug in the exact 6 o'clock position so as to fully purge the hot contaminated used oil. Rotate the wheel to the 5 or 7 o'clock position using the DPI. The DPI is magnetically attached to the hub pointing to the drain port. The DPI then sends wireless signals to an LED indicator enabling the operator to stop for example at the exact 5 o'clock position.
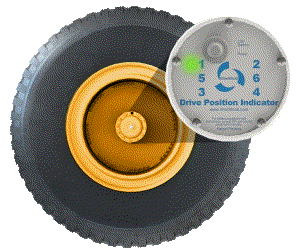
Mid Cycle, the DPI makes it easy to rotate the wheel and the LEM plug up to a high vent position to remove the plug to quickly check for steel or iron particles.
The DPI has proven to be invaluable in avoiding repeated trips up and down to and from the cab just to line up the plug(s) in the correct position for servicing. Reducing the travel up and down minimizes the wear and tear on operator's knees and avoids potentially costly slips and trips especially in wet conditions. Using the DPI onsite allows servicing to be done off-hours faster, with or without a 2nd person.