The base of any good oil analysis program is having the proper practices and procedures in place to take a representative oil sample. The results from your sample are what will determine if corrective actions need to be taken. An improper sample can skew results, producing either costly false negatives or false positives. Ultimately those improper samples can cause an oil analysis program to be abandoned.
A proper oil sample represents the true condition of the equipment. A proper sample should be taken while the equipment is running, from the same location, in the active zone every time. By definition, taking a proper oil sample seems simple but many companies are engaging in improper sampling practices-either by using poor sampling methods or procedures.
Following poor sampling methods and practices can be costly, and time-consuming. For instance, taking a drop tube or gravity driven drain sample can be inconvenient and unsafe. With both these methods, sampling with the equipment running is extremely dangerous to both the technician and the life of the equipment. Waiting for a shutdown in order to take the sample is not always convenient, and can lead to an undiagnosed problem worsening. When taking the sample using the drain method, the flow of oil cannot be controlled. This can lead to extra costs for topping up with new oil or possibly lead to machine starvation from lack of oil. Technicians must be careful to not get burnt from the hot oil. With both methods the only safe way to sample is by shutting off the machine and waiting for the oil to cool to a safe handling temperature which allows for more wear particles to settle. For trending results, it is recommended to sample from the same spot every time which is nearly impossible with these two methods. In the end, any drop tube or gravity driven drain sample will be unrepresentative of the true condition of the machine.
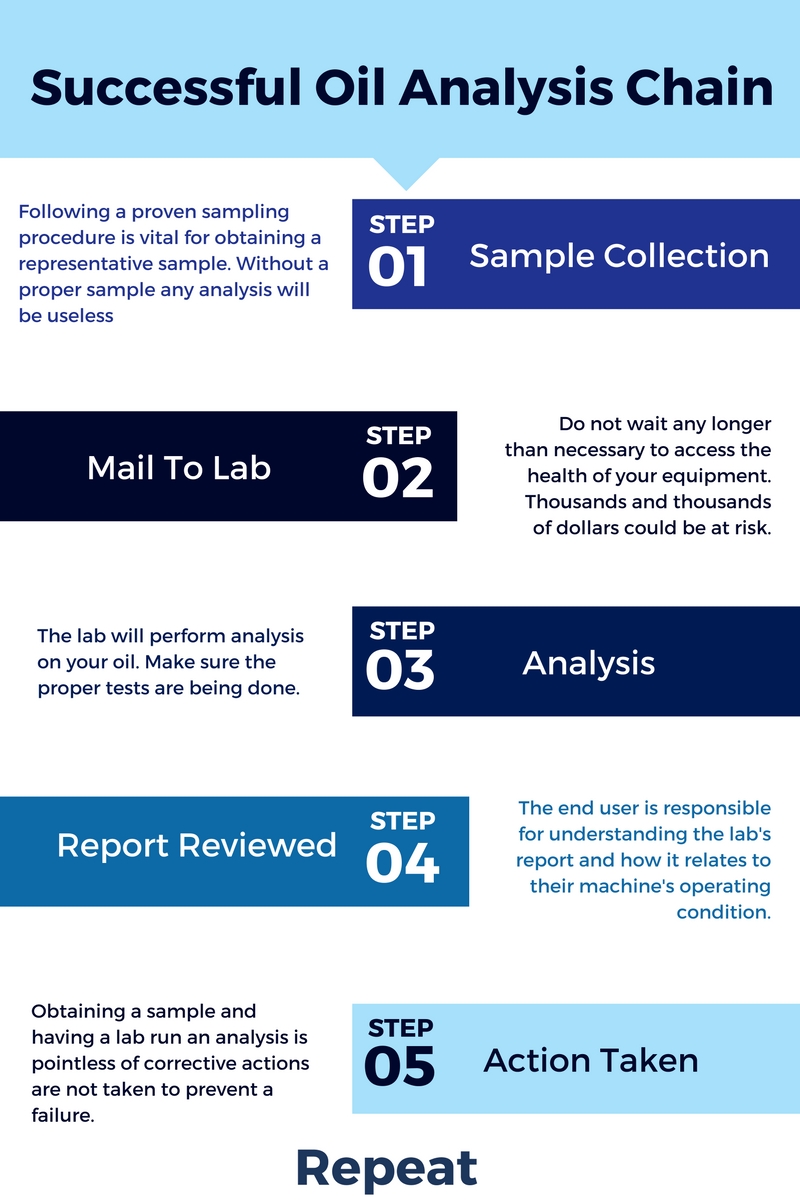
Sampling valves are the best method for obtaining proper, reliable oil samples. To start, sampling valves make it possible to take oil samples safely, while the equipment is running, from the same spot, every time. This means that oil samples can be taken at any time since shutdowns are no longer necessary. Sampling while the equipment is running ensures that the sample is a direct representation of the equipment's condition. Additionally, the oil sample is coming from the same spot in the active zone every time, away from the sediment and filters. Meaning that the sample pulled will contain hot information rich oil that can be trended against previous samples to show the condition of your equipment.
A world class oil analysis program starts with good practices and procedures to extract the most representative oil sample. The resulting data from a good oil sample will hold more useful information on the health of the equipment. These results will give teams the information needed to maximize reliability, reduce unplanned downtime and eliminate catastrophic failures.
Click to Download as a PDF