Much like the human body, machines need regular inspections to ensure that they are running properly. The best way for companies to check on the health of their equipment is through oil analysis. In the simplest sense, oil analysis, is a laboratory's breakdown of a lubricant's properties, contaminants, and wear debris. A technician or operator collects oil samples from their machines, sends the samples off to a laboratory, and then the lab compares the sample to previous samples. What results is meaningful information about the oil and equipment.
This oil breakdown allows for equipment operators to find defects in their equipment that would not be found through other sensory detection methods while the machine is in normal operating conditions. With this knowledge, operators can make the necessary adjustments to keep their equipment running at peak performance and plan for maintenance in advance.
There are three major reasons to take up an oil analysis program:
1) To predict impending machine failure more accurately
2) To diagnose past failures
3) To know when an oil change is necessary
To Predict Impending Machine Failure
Just like the human body, a machine can still run once a "failure" has occurred. But without proper treatment and diagnosis, it becomes only a matter of time before the machine fails entirely. As the machine's health begins to decline and it progresses down the PF Curve the cost of repair only becomes more expensive.
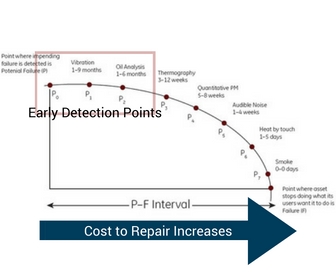
An advanced oil analysis program can sample and analyze suspended particles in the oil and then reveal specific individual component wear early in the deterioration phase. This early detection allows for the necessary individual parts to be obtained and the infect component fixed before a major failure occurs.
With an oil analysis program you become proactive in monitoring your equipment's health instead of only reacting to major problems. Being proactive in determining lubrication problems is much less expensive than allowing excessive friction to ruin a piece of equipment.
To Diagnose Past Failures
Much like the results of an autopsy on an uncertain death, a detailed oil analysis report can provide clarification on what components failed. Knowing what the wear particles are made of, where they came from, and how severe they are can give operators and technicians an exact cause of a machine's death.
Typically when a machine fails all evidence of the failure is destroyed along with the component. The absence of good evidence is what can lead to poor and costly decisions, like the implementation of preventative maintenance procedures that don't address the root problem. Fortunately, the evidence of component failure can still be found in lubrication even after the failure event has occurred. This evidence lets you know if the event was/is addressable or if it was random
To Know When an Oil Change is Necessary
Much like an annual checkup, a proper oil analysis will give you a detailed breakdown of your oil's performance. Accurate sample data allows many equipment operators to achieve condition based versus time-based oil changes. This maximizes uptime without compromising equipment health.
Regular oil analysis and reliable sampling of all major systems allows for critical decision planning of useful remaining life for each component and machine. With oil analysis, you'll know when to repair, when to overhaul, and when to keep or replace a machine regardless of service hours. In the end, this will save downtime and resources to restore the equipment.
Click to Download as a PDF